All Inclusive – PRIDE Industries Is Helping Employees with Disabilities to Succeed
PRIDE Industries is the United States’ leading employer of people with disabilities and those with other barriers to employment, including veterans and former foster youth. PRIDE Industries offers job training, placement, on-the-job coaching, and skills development for independent living. They have held IPC membership since 2000.
IPC Community talked to PRIDE Industries' Darelyn Pazdel, VP, Workforce Inclusion, and Andrew Williams, Director of Product Engagement, about PRIDE Industries’ manufacturing services division, and their interest in IPC workforce training programs. We also heard from George Hadley, Production Manager, and wire harness assemblers Khai Xiong and John Xiong about PRIDE Industries’ use of IPC Subscription Services for workforce training.
What is the size of the PRIDE Industries staff?
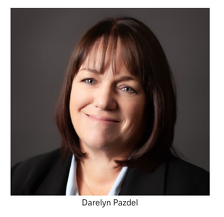
Darelyn Pazdel: PRIDE Industries has nearly 4,500 employees. About 2,000 of these individuals have a disability. We have a team of 425 people who assist individuals with disabilities in securing employment both within PRIDE Industries and in the community.
PRIDE Industries operates across several states – does it have a physical building in each of those states? How many of these companies include electronics manufacturing facilities?
Pazdel: PRIDE Industries 37 offices in 17 states throughout the United States. In some communities, we operate as a true integrated model, meeting people in their communities. Our flagship electronics manufacturing facilities are in Roseville, California, where we are unique in the industry, producing quality electronics and supporting a disability-inclusive team.
How did PRIDE Industries create employment specific to electronics manufacturing for individuals with disabilities?
Pazdel: Individuals with disabilities are successful in many industries. Given our nearly 60 years of experience with our mission to create employment for people with disabilities, it’s what we do naturally. Our team works with our employees to provide tools for accommodation. It is our experience that the learning curve may be a little steeper for individuals with disabilities, however, once they learn tasks and have the tools necessary, they deliver high-quality services and products. Electronics manufacturing for individuals with disabilities has been a natural fit for our organization. When you say that there are support systems in place for employees with disabilities, what does that mean? How do you obtain employees? Do you work closely with schools in your area?
Pazdel: Support systems for employees with disabilities can be both informal and formal. We strive to create an atmosphere where co-workers provide informal support, and we also have a team of trained job coaches. A job coach is someone who can provide formal support to an individual who may need to learn a new task, or who may need support with communication or soft skills.
We find our employees through many avenues. One way is meeting with high schools in the area and finding transition-aged students who are interested in employment. We also work with individuals who may have been referred to our employment services through the state vocational rehabilitation services. PRIDE Industries provides programs where we begin with the smallest of learning environments, for example, how to use public transportation, and we help them enhance their vocational skills from there. Employees have support throughout their employment journey with PRIDE Industries, and they are given the opportunity to learn and develop skills, increasing their confidence and independence.
PRIDE Industries placed nearly 300 individuals in other organizations, some of whom were in other EMS companies. We do not necessarily count success in numbers, however. When one individual is successful in an industry, we see this as an opportunity to replicate the effort.
How are you active in the community? Do you attend and recruit at local high schools or veterans affairs organizations?
Pazdel: PRIDE Industries is active in all communities where we operate and serve individuals. We work directly with local high schools, meeting with transition students who have disabilities or significant barriers to employment. We provide pre-employment training and offer internships and employment placement assistance. PRIDE Industries has our very own veteran's liaison that actively performs outreach to veterans in the community and provides support, matching veterans to PRIDE Industries opportunities.
Provide an example of how PRIDE works with members of the foster community.
Pazdel: PRIDE Industries works with the foster community through the high schools as well as through our Career Hub in Citrus Heights, California. This is a walk-in career center where many foster youth are referred to us through the County of Sacramento specifically for employment development.
How has your work changed over the years as the industry becomes more aware of the benefits of reaching out to the communities of veterans, individuals with disabilities, and those formerly in the foster system?
Pazdel: Our industry has grown and will continue to grow as we become stronger allies for people with disabilities. Each employer that we can educate on the benefits of hiring people with disabilities, veterans, and emancipated foster youth, is a new story created to be shared in their professional circles. We know that his model works, and we’ve grown the model with each successful employment match.
Our future success is bright as we continue to prepare people for employment and then provide the support they may need and support for employers to understand their skills and how to welcome this skilled workforce onto their teams.
Workforce Training at PRIDE Industries
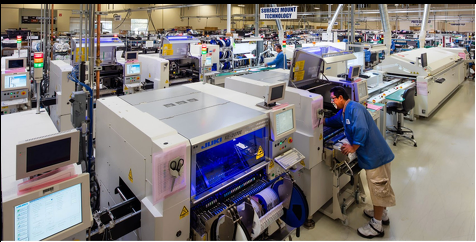
You recently purchased a workforce training subscription from IPC. How do you think this training will benefit your employees overall, and your employees with disabilities?
Andrew Williams: When we evaluated the program, we listed the benefits that we required. We believe these will be greatly recognized over this first year.
- Increasing the level of quality on the floor by improving operator knowledge.
- Gaining IPC-level training courses for all electronics manufacturing staff.
- Increasing the ability to recognize advanced operators to send for certification classes
- Strengthening our abilities for J-STD-001 (Mil-Aero).
- Providing for additional factors to be marketed to potential customers via a stronger workforce.
- Assisting with maintaining a competitive edge without having to invest in a full-blown training/certification program that can be very costly and requires an internal training administrator to control.
From the aspect of our employees with disabilities, this training package gives us a stable platform to provide higher level training that would otherwise be very difficult to establish without a dedicated training coordinator just for the electronics manufacturing services division. Being able to group employees for specific training classes will also enable us to schedule content review meetings to ensure that everyone has ample opportunity to get help with any areas they may have trouble with.
Why did you choose IPC’s training subscription service?
- There are multiple reasons for selecting the IPC Training subscription, but the key items are:
- All courses are online, and self-paced, and students have access to content for 90 days.
- Several courses are great for establishing the baseline of determining candidates to pursue operator certification for IPC-610, IPC-620, and J-STD-001.
- Multiple lower-level courses have been released to assist with the onboarding of non-industry employees.
- Without a Certified IPC Trainer on staff, a robust training system for industry training was needed (we have a solid training system for ISO/general/HR items, but it does not include higher level training for the electronics manufacturing industry).
The program has been in place for six weeks now, what has the feedback been?
So far, the feedback has been very good. A decent range of positive comments related to the intensity and quality of the content. The training is driving a lot of discussion with staff on our production floor as they navigate the training in the same timelines.
How are participants responding to the IPC courses?
George Hadley: The feedback I have received has been very positive. The amount of detail that is in the courses is very good and relevant to what we do. The only fear expressed by the employees is not being able to pass the quiz by the third time taken. My response to that has been to take notes as you go through each section, hearing the content and writing it down will help with retaining it.
Khai Xiong and John Xiong are wire harness assemblers currently enrolled in the IPC workforce training course. We asked them about their experiences.
Three Employees Share Their Thoughts
Why did you choose to take the training course?
Khai: I chose this training course because I want to learn new skills and develop existing ones.
John: It was in my best interest to expand my knowledge and have a deeper understanding of electronics.
Armand: I wanted to learn more about electronics manufacturing.
Please explain how the course helps you do your work at PRIDE.
Khai: This course gave me more knowledge and helped me to minimize time working on electronics to produce more quantity with high quality at PRIDE Industries.
John: It has helped me strengthen my skill levels and improve on achieving higher quality and quantity.
Armand: The course is connected to my every day tasks. I have learned news skills and techniques to handle products.
Is the content of the course helpful? Do you have suggestions for improvement?
Khai: All the content of the course is very helpful. All the videos and pictures are excellent, helping me get a better understanding of the course. No suggestions for improvement.
John: Yes, the content was very helpful. No other suggestions.
Armand: Yes, because I can do it on and off during working hours.
Is the self-paced, online module helpful to you?
Khai: The self-paced online module is very helpful to me; it gives me more time and it's great that I can go back to the module when I need to review again.
John: Yes, having the flexibility to take the courses on my own time is very helpful.
This article was previously published in IPC Community.