Electronic Essentials: What You Think You Know - and More
This webinar, titled "Electronic Essentials: What You Think You Know - and More", is a foundational session aimed at reinforcing the core knowledge that every technician, inspector, assembler, operator, and engineer in electronics manufacturing should possess. These are the essentials of quality and reliability in electronics manufacturing—the things you should know without flipping through an IPC standard. Whether you're new to the field or a seasoned pro, this session is your checklist for baseline competency. Knowing these terms without referencing IPC standards demonstrates professional readiness and process awareness and supports faster troubleshooting, better communication, and supports a better team culture.
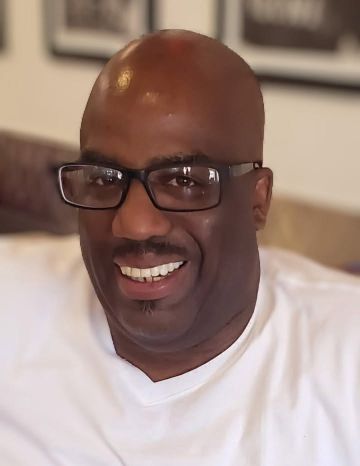
Speaker Bio:
With over 44 years of experience in the aircraft and spacecraft industry, Greg Merrill brings a wealth of knowledge and hands-on expertise to the field. He served in the U.S. Air Force for eleven years, where he was a key team member in the CFM engine conversion for the KC-135 and contributed to several high-profile and classified programs, including work at Area 51 and on the F-117 Stealth Bomber. Notably, Greg was the fifth electrician selected Air Force-wide—and the lowest-ranking—to work on a top-secret program. He also supported the Airborne Command Post, a critical component of the Air Force’s nuclear readiness mission.
After transitioning to the civilian sector, Greg continued to contribute to groundbreaking aerospace projects in roles ranging from technician and engineer, source inspector, and currently a MIT and consultant with Electronic Training Solutions. His civilian accomplishments include work on the Android satellite constellation, development of a fuel latch valve for first-generation satellite systems, and the design of a power supply for astronauts’ space suits—supporting life support systems and helmet lighting. He also contributed to the Solar Array Drive Assembly (SADA) for the International Space Station, which controls the movement of solar panels, and the Joint Polar Satellite System (JPSS), which monitors global weather patterns.